基板(PCB)とは、電子部品を配置し、導体回路で接続する電子製品の中核となる部品です。PCBは、ガジェットや家電製品から医療機器や航空宇宙産業まで、とても幅広い分野で使用されています。近年の技術革新により、基板はさらに高性能化・小型化が進み、様々な産業で重要な役割を担っています。
基板は一般的にガラスエポキシやFR-4と呼ばれる素材で作られており、多層化や表面実装技術(SMT: Surface Mount Technology)によって部品実装の効率が向上しています。さらに、リジッド(硬い)基板やフレキシブル(柔らかい)基板といった形状や用途に応じたタイプが存在します。これにより、デバイスの形状や性能のニーズに合わせて適切な基板設計が可能となっています。
基板製造のプロセスは非常に精密で複雑であり、PCB設計、製造、組立、検査の各ステージが密接に関連しています。製造过程中に精密な機械や特殊な化学物质が使われるため、質の高い基板を生産するためには一貫した品質管理と高い技術力が求められます。今後も基板技術の進化が産業全体のイノベーションを牽引していくことでしょう。
基板PCBの基本概念
基板PCBは、電子機器で使用される基本的な部品であり、様々な種類や材料が存在します。それぞれの要素について詳しく見ていきましょう。
定義
基板PCB(Printed Circuit Board)は、電子部品を搭載し、それらを配線で接続するための基板です。これにより、電子機器の小型化や信号品質の向上が可能となります。
種類
基板PCBにはいくつかの種類があります。
- シングルサイド基板: 配線が基板の片面にしかないタイプ
- ダブルサイド基板: 配線が基板の両面にあるタイプ
- マルチレイヤー基板: 複数の配線層を持つタイプ
また、基板の厚さやサイズ、形状なども異なります。
材料
PCBの材料には、以下のようなものがあります。
- FR-4: 繊維強化エポキシ樹脂。一般的に最もよく使われる材料です。
- アルミニウム: 熱伝導性が良く、放熱に適しています。
- セラミック: 高周波回路や高温環境下での使用に適しています。
以上が基板PCBの基本概念についての説明です。これらの知識を活用して、適切な基板を選定しましょう。
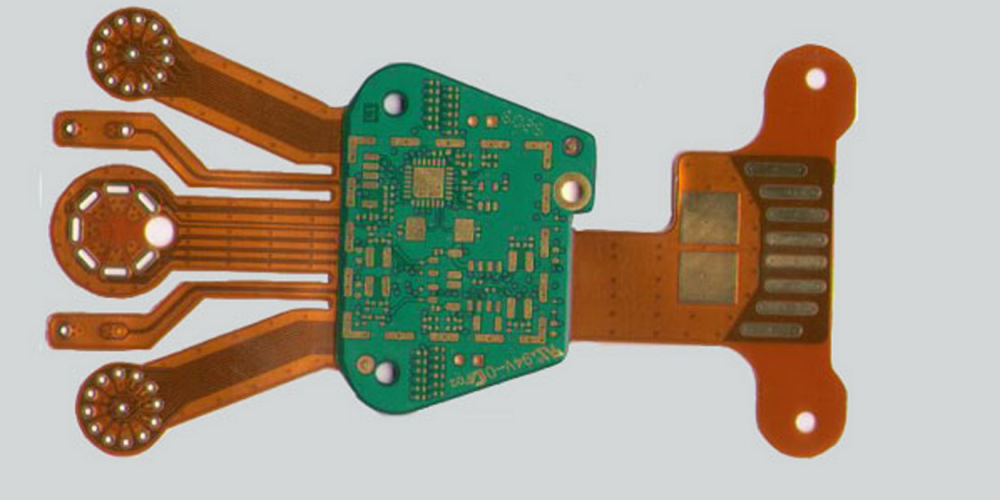
基板PCB設計のプロセス
回路設計
基板PCB設計の始めに行う手順は、回路設計です。まず、設計する基板の回路機能を考慮し、電子部品を選定します。
- 電子部品選定
- 抵抗
- コンデンサ
- 基本的なIC
次に、電子部品間の接続方法を決定し、回路図を作成します。回路図は、基板設計ソフトウェアを利用します。
レイアウト設計
回路設計が終わった後、基板のレイアウト設計を行います。レイアウト設計では、回路図に記載された電子部品を基板上に配置し、パターン(配線)を設計します。重要なポイントは以下の通りです。
- 信号配線の長さ調整
- 高周波回路の影響を避ける
- 電源配線の最適化
基板設計ソフトウェアを使用して、レイアウトを確認し、最適な設計ができます。
ガーバーデータ作成
レイアウト設計が完了したら、次はガーバーデータを作成します。ガーバーデータは、基板製造業者が利用するデータフォーマットで、基板の回路やパターンの情報が記載されています。
作成されたガーバーデータは、基板製造業者へ送付し、基板が製造されます。基板の製造が終われば、表面実装やスルーホール実装などの方法で、回路設計に従って部品を実装し、基板PCBが完成します。
基板PCB製造工程
銅箔積層
基板PCB製造の最初の工程は、銅箔積層です。これにより、基材に銅箔が貼り付けられ、回路パターンが形成されます。一般的な手順は次のとおりです。
- 基板素材を選択し、銅箔を基材に貼り付けます。
- 必要に応じて複数の層を重ねます。
この過程では、基板の種類や厚さ、銅箔の厚さなどを考慮する必要があります。
銅箔エッチング
次に、銅箔エッチング工程が行われます。この工程では、不要な銅を除去して回路パターンを作成します。エッチングには、酸性またはアルカリ性の薬剤が使用されます。主なステップは以下の通りです。
- 回路パターンのマスクを適用します。
- 薬剤で銅の表面をエッチングし、マスクされていない部分を除去します。
エッチング工程は、正確な回路パターンを作成するために、非常に重要です。
穴あけ
穴あけ工程では、基板に穴を開け、異なる層やコンポーネントを結びつけます。穴あけには、機械的ドリルやレーザードリルなど、さまざまな方法があります。
- 穴あけマシンで基板に穴を開けます。
- 開けられた穴の位置とサイズを確認します。
プレート処理
穴あけ後、プレート処理が行われます。この工程では、穴の内部に銅を付着させて導電性を確保し、異なる層を電気的に接続します。
- 基板を化学溶剤に浸し、穴の内部を銅でコーティングします。
- 必要に応じて、さらに金やニッケルなどのメッキを行います。
印刷配線板検査
最後に、製品の品質を確保するために、印刷配線板の検査が行われます。検査方法には、視覚検査、自動光学検査(AOI)、X線検査などがあります。
- 実装前の基板の外観や配線の確認を行います。
- 問題が見つかった場合は、修正や廃棄が行われます。
これらの工程を経て、基板PCB製造が完了します。

組み立てと実装技術
表面実装技術(SMT)
表面実装技術(SMT、Surface Mount Technology)は、電子部品を直接基板の表面に実装する技術です。SMTは以下の技術分類に分けられます。
- リフロー実装
- ウェーブ実装
- ディスペンサー付け
リフロー実装は、半田ペーストを基板に塗布し、部品を配置して加熱して半田を溶かすことで部品が固定されます。
ウェーブ実装は、部品の足に半田メッキをし、基板にウェーブ状に半田を流すことで基板と部品が接続されます。
ディスペンサー付けは、精密な位置に半田ペーストを付けることができ、熱に弱い部品にも適しています。
穴実装技術(THM)
穴実装技術(THM、Through Hole Mount)は、電子部品の端子を基板にあらかじめ開けられた穴に挿入し、裏面から半田で固定する技術です。THMの主な技術分類は以下の通りです。
- 手作業実装
- 自動挿入実装
手作業実装は、技術者が部品を挿入し、半田付けを行う方法で、少量生産や試作品に適しています。
自動挿入実装は、専用のマシンが高速で部品を挿入し、半田付けを行う方法で、大量生産に適しています。
SMTとTHMは、それぞれ特性が異なるため、用途や製品に応じて適切な実装技術を選択することが重要です。
品質試験と検証方法
基板PCBの品質試験と検証方法は、信頼性を確保し、問題を特定するために非常に重要です。このセクションでは、ビジュアル検査、自動光学検査(AOI)、およびX線検査といったいくつかの一般的な検証方法について説明します。
ビジュアル検査
ビジュアル検査は、基板PCBの表面上の不具合を目視で確認する最も単純な方法です。この方法の主な目的は、次のような問題を特定することです。
- 配線の欠陥
- ソルダーの肩
- パッドの破損
- コンポーネントの配置が間違っている
専門家は、しばしば顕微鏡を使用して、より小さな不具合を確認するためにビジュアル検査を行います。
自動光学検査(AOI)
自動光学検査(AOI)は、ビジュアル検査のより高度な形態であり、カメラと画像処理アルゴリズムを使用して基板上の欠陥を検出します。AOIのメリットは、以下の点です。
- 高速かつ正確: 画像解析アルゴリズムの使用により正確な結果を早く得ることができます
- 再現性: 同じ条件で何度でも試験を行うことができます
- 人間の目の限界を超えた検査: カメラと顕微鏡を組み合わせることで、人間の目では確認できない欠陥も検出できます
X線検査
X線検査は、基板の内部構造を調査するために使用される別の検証方法です。この方法の利点は、以下の点です。
- 非破壊検査: 基板を破壊することなく内部を調査できます
- 隠れた欠陥の検出: 表面検査では見えない欠陥、例えば内部ショートやデラミネーションも検出できます
X線検査は、主にBGA(Ball Grid Array)やQFN(Quad Flat No-Lead)などの隠れたソルダージョイントを持つコンポーネントの検査に使用されます。

基板PCBの環境への影響と廃棄物処理
基板PCB(プリント基板)は、電子機器の製造において不可欠な部品ですが、その製造および廃棄時に環境への影響があります。
まず、基板PCBの製造過程においては、銅や鉛などの金属材料の加工が伴うため、これらの金属の採掘や精錬から生じる環境負荷が考えられます。さらに、基板製造時には樹脂や化学薬品の使用も必要で、これらの物質が環境や労働者の健康に与える影響も懸念されます。
一方、基板PCBの廃棄物処理においても、問題があります。使用済みの電子機器や廃棄される基板PCBには有害物質が含まれており、これらが適切に処理されないと土壌や水質の汚染が引き起こされる可能性があります。特に、一部の開発途上国では適切な廃棄物処理が行われていないことが問題となっています。
現在、環境への影響を軽減するために以下の取り組みが行われています。
- 製造過程での金属採掘や精錬時の環境汚染対策強化
- 労働者の健康管理や化学物質の取り扱い改善
- 基板PCBに使用する材料のリサイクルや環境に優しい代替品の開発
- 電子機器のリサイクルや廃棄物処理の適正化推進
以上のように、基板PCBの製造および廃棄物処理に関連する環境への影響に対処するために様々な取り組みが進められていますが、今後も継続的な改善が求められるでしょう。