プリント基板の製造工程は、電子機器の製造に欠かせないものです。プリント基板は、電気回路を構成するために用いられる基板であり、印刷技術を用いて製造されます。プリント基板は、小型化・高性能化が進む現代の電子機器において、ますます重要性を増しています。
プリント基板の製造工程は、主に以下のような工程から構成されます。まず、基板の素材を選定し、必要に応じて表面処理を行います。次に、回路設計に基づいて、回路を形成するためのパターンを作成します。その後、パターンを基板に転写し、化学反応によって回路を形成します。最後に、必要に応じて表面処理を施し、電気的性能を調整します。
プリント基板の製造工程は、高度な技術と手作業によって行われます。製造工程の正確性が求められるため、品質管理が非常に重要です。また、省エネルギー・環境保護などの観点から、製造プロセスの改善が進められています。
プリント基板の製造工程の概要
基板の設計
プリント基板の製造工程は、まず基板の設計から始まります。基板の設計は、回路図をもとに行われ、CADソフトウェアを使用して行われます。基板の設計には、回路の配線、部品の配置、基板のサイズ、厚さなどが含まれます。
フォトリソグラフィー
基板の設計が終わったら、次はフォトリソグラフィー工程に進みます。この工程では、基板に光感受性のレジストを塗布し、回路図のパターンを転写するためのマスクを作成します。マスクを基板に載せ、紫外線を照射することで、レジストを硬化させます。
エッチング
フォトリソグラフィー工程が終わったら、次はエッチング工程に進みます。この工程では、レジストが硬化したパターン部分を残し、基板表面から不要な部分を削除します。エッチングには、化学的な方法と物理的な方法がありますが、一般的には化学的な方法が使用されます。
メッキ
エッチング工程が終わったら、次はメッキ工程に進みます。この工程では、基板表面に金属をコーティングし、回路を保護します。メッキには、銅、ニッケル、金などが使用されます。
印刷
メッキ工程が終わったら、次は印刷工程に進みます。この工程では、基板に部品の実装位置を示すシルク印刷が行われます。シルク印刷は、一般的に白色のインクを使用します。
実装
最後に、基板に部品を実装する工程に進みます。この工程では、部品を基板にはんだ付けします。はんだ付けには、手作業と機械作業の両方があります。
以上が、プリント基板の製造工程の概要です。
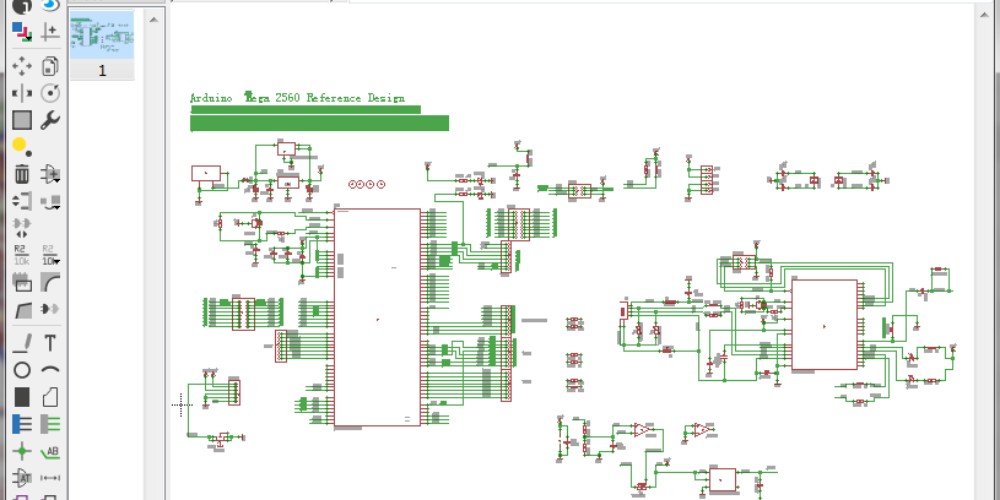
基板の設計
回路図の作成
基板の設計において、回路図の作成は非常に重要です。回路図は、基板のレイアウト設計やガーバーデータの生成に必要な情報を提供するため、正確で詳細な回路図を作成することが必要です。
回路図の作成には、回路図エディターを使用することが一般的です。回路図エディターは、回路図を直感的に作成できるため、作成時間を短縮できます。また、回路図エディターは、回路図の検証機能を備えていることが多く、回路の動作を確認することができます。
レイアウトの設計
回路図の作成が完了したら、次に基板のレイアウト設計を行います。レイアウト設計では、回路図上の部品を基板上に配置し、部品同士を接続するための配線を設計します。
レイアウト設計には、基板設計ソフトウェアを使用することが一般的です。基板設計ソフトウェアは、部品の配置や配線のルーティングを自動的に行うことができます。また、基板の外形や厚みを設定することもできます。
ガーバーデータの生成
レイアウト設計が完了したら、最後にガーバーデータの生成を行います。ガーバーデータは、基板製造工場で基板を製造するために必要なデータです。
ガーバーデータは、基板設計ソフトウェアから出力することができます。ガーバーデータには、基板の各層の情報や、部品の配置や配線の情報が含まれています。基板製造工場では、ガーバーデータを基に基板を製造します。
以上が、基板の設計における回路図の作成、レイアウト設計、ガーバーデータの生成についての説明です。
フォトリソグラフィー
感光剤の塗布
フォトリソグラフィーは、プリント基板の製造において非常に重要な工程です。この工程では、感光剤をプリント基板に塗布します。感光剤は、光を当てることで化学反応を起こし、プリント基板上にパターンを形成する役割を担っています。
マスクの配置
次に、マスクをプリント基板の上に配置します。マスクは、感光剤が塗布された部分と塗布されていない部分を区別するために使用されます。マスクには、プリント基板に形成したいパターンが描かれています。
露光
マスクが配置された後、プリント基板を露光装置にセットします。露光装置は、マスクに描かれたパターンに沿って、光を照射することで感光剤を活性化します。この工程によって、プリント基板にはマスクに描かれたパターンが転写されます。
現像
最後に、現像液を使用して感光剤を現像します。現像液は、感光剤が活性化された部分を溶かし、プリント基板上にパターンを形成します。この工程によって、プリント基板にはマスクに描かれたパターンが確実に形成されます。
以上が、フォトリソグラフィーの工程になります。この工程を正確に行うことで、高品質なプリント基板を製造することができます。

エッチング
腐食液の準備
エッチングは、プリント基板の製造工程の中でも重要な工程の一つです。この工程では、腐食液を使用して不要な部分を削り取り、必要な回路を形成します。腐食液は、酸性またはアルカリ性の液体であり、プリント基板に適した腐食液を選択することが重要です。
腐食液を準備する際には、以下の点に注意する必要があります。
- 安全性に配慮する
- 濃度を正確に調整する
- 温度を管理する
腐食液によるエッチング
腐食液によるエッチングは、プリント基板の表面を削り取り、回路を形成するための重要な工程です。この工程では、腐食液がプリント基板の表面に接触することで、不要な部分が削り取られます。
腐食液によるエッチングを行う際には、以下の点に注意する必要があります。
- 腐食液の濃度を正確に調整する
- 腐食液の温度を管理する
- エッチング時間を正確に管理する
残像の除去
エッチングが完了すると、プリント基板には回路が形成されますが、不要な残像が残ることがあります。これらの残像を除去するために、残像除去工程が必要です。
残像除去工程では、アルカリ性の溶液を使用して、不要な残像を除去します。この工程を行う際には、以下の点に注意する必要があります。
- 溶液の濃度を正確に調整する
- 温度を管理する
- 残像除去時間を正確に管理する
以上が、エッチング工程についての説明です。
メッキ
金属の蒸着
プリント基板のメッキは、基板上に金属を蒸着させることで行われます。金属は真空中で蒸発させ、基板表面に付着させます。蒸着する金属は、主に銅、ニッケル、および金です。
めっき液の準備
メッキ液は、メッキ対象となる金属イオンを含む溶液です。メッキ液の準備は、メッキ対象となる金属によって異なります。一般的には、メッキ液には金属イオン、還元剤、界面活性剤、およびpH調整剤が含まれます。
電気化学反応によるメッキ
プリント基板のメッキは、電気化学反応によって行われます。基板は陽極として、メッキ液に浸された金属板は陰極として接続され、電流を流します。この電流によって、メッキ対象となる金属イオンが還元され、基板表面にメッキが形成されます。
以上が、プリント基板のメッキについての概要です。
印刷
印刷機の準備
プリント基板の印刷工程は、印刷機を使用して行われます。印刷機は、基板にインクを塗布するために使用されます。印刷機を使用する前に、以下の手順を実行する必要があります。
- 印刷機のセットアップ
- 印刷機のキャリブレーション
- インクの準備
インクの塗布
印刷機が準備できたら、次にインクを塗布する必要があります。インクは、基板に均一に塗布する必要があります。以下の手順に従って、インクを塗布します。
- インクを印刷機のローラーに塗布します。
- 基板を印刷機の上に置きます。
- 印刷機をスタートさせ、基板にインクを塗布します。
乾燥
インクが塗布されたら、基板を乾燥させる必要があります。乾燥は、インクが基板に十分に固定されるために必要です。以下の手順に従って、基板を乾燥させます。
- 印刷機から基板を取り出します。
- 基板を乾燥室に置きます。
- 基板を乾燥室で乾燥させます。
以上が、プリント基板の印刷工程についての概要です。
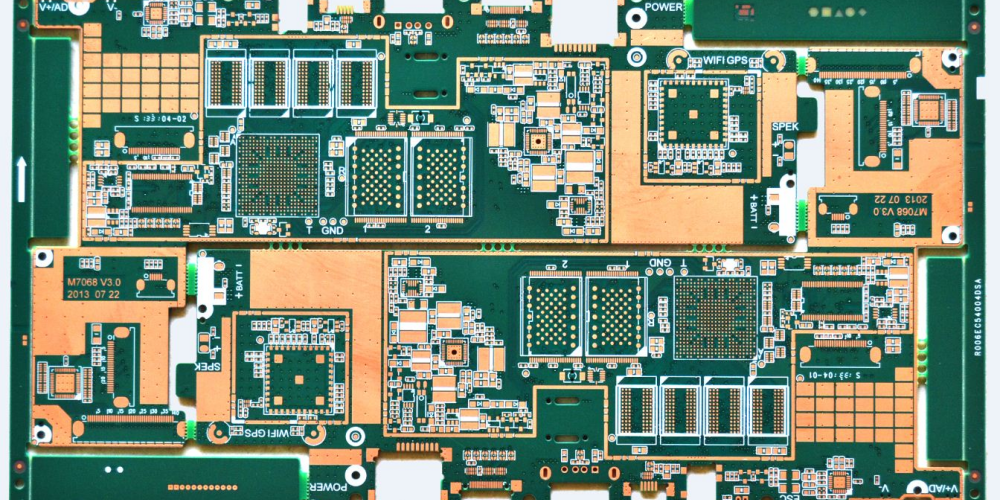
実装
部品の選定
プリント基板の実装において、部品の選定は非常に重要です。適切な部品を選択することで、信頼性の高い製品を作ることができます。部品の選定には、以下のような要素が考慮されます。
- 部品の性能
- 部品の寿命
- 部品のコスト
- 部品の供給状況
これらの要素を考慮して、最適な部品を選定する必要があります。
部品の実装
部品の実装は、プリント基板の実装において最も重要な工程の一つです。部品の実装には、以下のような手順があります。
- 部品の位置を決定する。
- 部品を基板に取り付ける。
- 部品をはんだ付けする。
部品の位置を決定する際には、基板上に部品が干渉しないように注意する必要があります。また、基板の設計によっては、部品の位置が決まっている場合もあります。
部品を基板に取り付ける際には、部品の形状やサイズに応じて、以下のような方法があります。
- 手作業による実装
- 自動実装機による実装
部品をはんだ付けする際には、はんだ付けの品質に注意する必要があります。はんだ付けの品質が低いと、信頼性の低い製品となってしまいます。
はんだ付け
はんだ付けは、部品を基板に取り付けるために必要な工程です。はんだ付けには、以下のような手順があります。
- 部品と基板の接点にはんだを塗る。
- はんだを溶かして、部品を基板に取り付ける。
- 冷却してはんだを固定する。
はんだ付けには、以下のような方法があります。
- 手作業によるはんだ付け
- 自動はんだ付け機によるはんだ付け
はんだ付けの品質には、以下のような要素が影響します。
- はんだの種類
- はんだの量
- はんだの温度
- はんだ付けの時間
これらの要素を適切に調整して、高品質なはんだ付けを行う必要があります。